Taysir Bader
The Art and State of Safety Journal Club
April 7th, 2021
The March 31 and April 7th Journal Club meetings discussed the article The Joint Safety Team at the University of Minnesota, Twin Cities: A Model for Student-Led Safety, which is available at https://pubs.acs.org/doi/10.1021/acs.jchemed.0c00153
Highlights from the table read discussion and the article are below. Taysir’s complete presentation can be downloaded here:
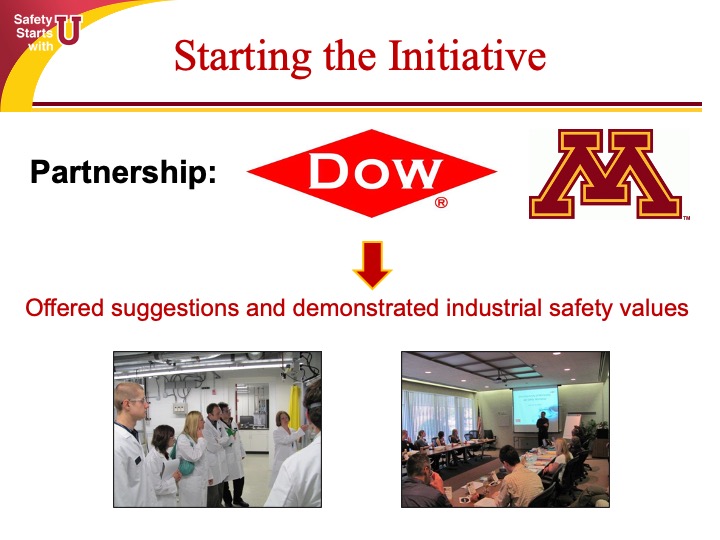
The Joint Safety Team (JST) was an initiative started by students from the Departments of Chemistry (CHEM) and Chemical Engineering and Materials Science (CEMS) with the aim of proliferating a culture of laboratory safety from a bottom-up approach via four main areas: compliance, awareness, resources, and education. The idea of the JST germinated from discussions between both departments, in addition to the Department of Environmental Health and Safety (DEHS) at the University of Minnesota with guidance from the Dow Chemical Company in 2012. The departments sought to embrace safety standards prevalent in industry while establishing a culture of safe practices in academic laboratories. Additionally, the JST team was expected to supplement the efforts of the faculty-led safety committees of the two departments to ensure compliance of laboratory practices with government regulations.
Since its initiation in 2012, the JST has taken great strides to be recognized as a leader in student-led safety. The safety endeavor has been well supported by the two departments which have enabled the JST to think of short and long-term safety goals. In 2015, as the initial members who had visited Dow were graduating, both department heads agreed to an ongoing investment in the organization to encourage committee participation and address some concerns from principal investigators about student time being taken away from research[a][b][c][d][e].[f][g][h][i][j][k]¨C11C¨C12C¨C13C¨C14C¨C15C The funding was utilized to provide stipends to JST committee members to ensure prolonged participation in the organization¨C16C¨C17C¨C18C. Furthermore, additional funding from the Dow Chemical Company and the Valspar Corporation (now Sherwin-Williams) was acquired in late 2015, which bolstered JST activities. The financial support from the departments and industrial partners has been critical for the ongoing success of the organization.
The current pyramid structure of the JST (Figure 1) is based on a strong foundation of volunteers[t][u][v][w][x][y] and laboratory safety officers (LSOs) who are responsible for daily implementation of safety practices in their respective research groups. Graduate students and postdoctoral associates assume the role of LSOs of individual laboratories by expressing their interest to the principal investigator of the research group and are assigned by the latter. Typically, laboratories involve two LSOs, a junior (first or second year student) and a senior (student in at least their third year or a postdoctoral associate) member of the group to enable efficient information transfer.
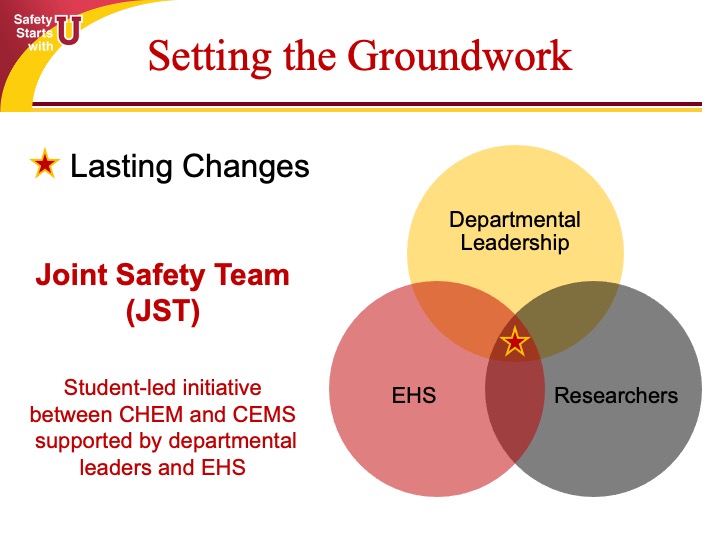
The Administrative Committee (AdCom) was formed as a part of the initial JST and included seven members in 2012. Presently, it is led by the president of the JST and includes the chairs of three subcommittees (E&R, A&C, PR), a Finance Officer, a Technology Officer, and representatives from the Department of Environmental Health and Safety (DEHS) at the University of Minnesota. After a collaboration with the Valspar Corporation (now Sherwin-Williams) was established in 2014, monthly AdCom meetings also included a representative from the company. The frequency of the meetings was chosen to ensure that the time committed by graduate students and postdoctoral associates to JST activities was limited and their primary focus lay in research. The member of the DEHS provides expert advice on policy and regulation issues regarding safety while the Sherwin-Williams representatives contribute industrial level expectations to strive toward. [z][aa][ab][ac][ad][ae][af][ag][ah][ai][aj]¨C36C¨C37C¨C38C¨C39C¨C40C¨C41C¨C42C¨C43C¨C44C¨C45C
The AdCom meetings create accountability for ensuring smooth functioning of the subcommittees and aim to provide vision and ideas for future events and activities. The members of the AdCom Committee identify departmental safety weaknesses that need to be addressed in the CEMS and CHEM departments. The president sets and enforces the agenda of all AdCom meetings and is responsible for filling the open positions in the subcommittees.
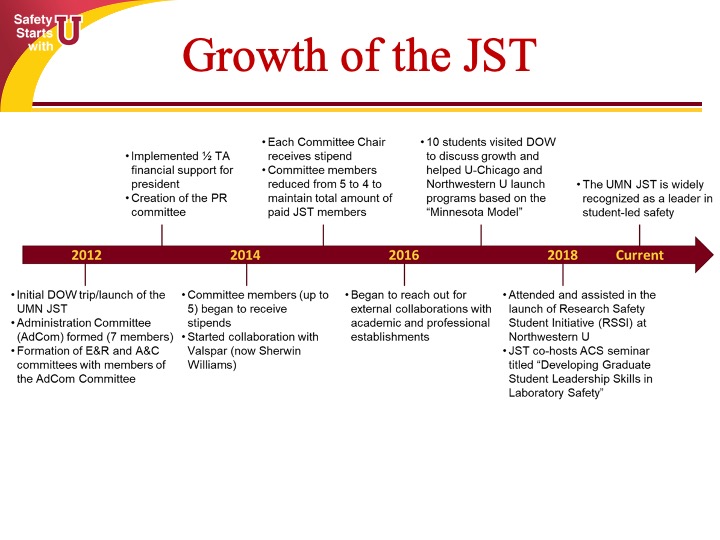
The JST website (www. jst.umn.edu) has been instrumental in communicating safety in the two departments, in addition to being the face of the organization as perceived by other research departments. The Technology Officer, in conjunction with the President, is responsible for website maintenance. The website contains access to the LSO guidebook via a university email address, which includes documentation for LSO training, roles and responsibilities, and transitioning between LSOs in a research group. It also includes “safety moments”, which are publicly available slides discussing specific aspects for widespread use among all researchers. Academic presentations in the CEMS and CHEM departments are preceded by a safety moment to instill a “safety first” attitude across students, postdoctoral associates, and faculty. The website also gives access to the Learning Experience Reports (LER) system. A sister manuscript details how LERs have contributed to improving academic safety in the two departments
The Finance Officer manages the JST expenses and projected budgets including printing and safety awards and also ensures enough funds are present. Additionally, the officer is also responsible for preparing the annual budget describing all expenses incurred, which helps the JST obtain future funding. The officer also contributes to AdCom discussions that are aimed at determining the financial feasibility of JST events and prizes. The expenses of the JST have varied through the years around a mean of $1500.[au][av][aw][ax][ay][az][ba][bb][bc][bd]
The Education and Resources Committee: The Education and Resources (E&R) committee oversees the organization of safety events for the LSOs of the CEMS and CHEM departments. The events are held every other month during the academic year and culminate into a grand annual safety event in August, open to all members of both departments[be][bf][bg][bh] (staff, graduate students, postdoctoral associates, and professors). The committee members (one chair, four paid members, and an unlimited number of volunteers) determine the topics of each event and are responsible for the content and the subsequent organization of the events. The E&R committee has evolved from its initial role of solely providing safety information to that of organizing events that train researchers in several practical aspects of safety. The first academic meeting held in October typically covers the roles and responsibilities of LSOs as the meeting coincides with the most frequent LSO transition period.
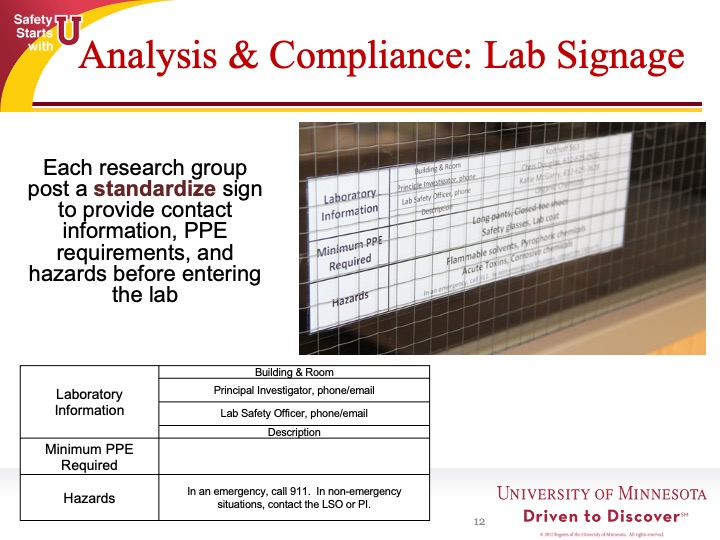
Topics covered at the other meetings change every time and have included round-table discussions and other interactive activities to engage and maintain the interest of the attendees. Often, we ask the participation of professors either for specific training or for sharing their approach to safety (e.g., evolution of safety over the years since the 1950s by an Emeritus Professor https:// youtu.be/HwXQPdhToec). Additionally, the E&R committee manages and updates the Laboratory Safety Officers’ guidebook. This document explains the roles and responsibilities of the LSOs in their laboratories and contains hyperlinks in order to effectively provide the LSOs with all the resources necessary to support them in their function. Feedback[bi][bj][bk][bl] from participants is constantly sought to gauge the interest generated by a specific safety training and its format as well as to determine safety topics of interest ensuring true peer contributions. We found that interactive and entertaining activities help deliver safety messages efficiently.
Analysis and Compliance: The Analysis and Compliance (A&C) committee is devoted to preparing methodologies which promote safe behaviors and work environment in individual laboratories. he A&C committee coordinates the biannual peer-to-peer safety walkthroughs of the 53 experimental research laboratories[bm][bn] within the CEMS and CHEM departments aimed at evaluating laboratory safety compliance. The committee also administers the departmental safety surveys to encourage dialogue involving safety within both departments. The safety walkthroughs are peer-to-peer safety inspections organized in October and April every year and conducted by the LSOs. For the fall walkthroughs, LSOs from three to four groups are randomly teamed up, whereas in the spring, teams are selected based on the hazard classification. By randomizing the teams, the LSOs are better informed about hazards which they do not commonly encounter. Consequently, they engage in safety discussions and learn how specific hazards are dealt with (e.g., radiation, large scale reactions, high pressure reactors, biological hazards). The reports are then shared with the respective principal investigators and discussed with researchers within individual research groups. Deficiencies are expected to be addressed before the next walkthrough. Even though these walkthroughs[bo][bp][bq][br][bs][bt] do not obligate any safety improvements, we have found that comments and suggestions are generally followed, and overall safety improvement has been observed and noted in the laboratories compared to previous walkthrough assessments. A comparison of the safety areas which “need attention” between 2012 and 2019 show that the number of laboratories showing inadequate levels of safety has drastically reduced (Figure 6).
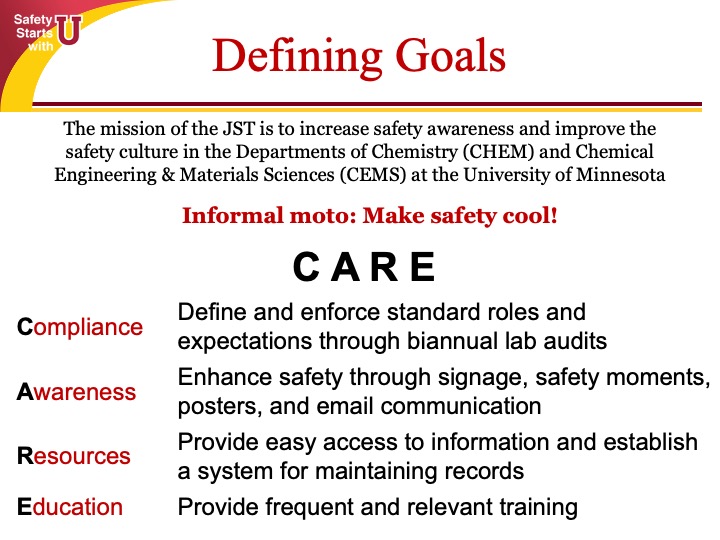
The A&C committee also conducts anonymous departmental safety surveys every semester including staff and faculty of both departments. The goal of these surveys is to obtain feedback about the general safety climate, specific aspects of laboratory safety, general suggestions, and for people to raise any other safety concerns. The results of the surveys are summarized and discussed with department heads for further discussion among the departmental faculty-led safety committees. For example, teaching assistants in the CHEM department had raised concerns about lack of adequate training for medical emergencies in a teaching laboratory setting. As a result, a step-by-step procedure highlighting the decisions to make and explaining the steps to take in the case of an emergency has been established and given to teaching assistants. [bu][bv]
Public Relations: The Public Relations (PR) committee was formed in 2013 as an addition to the E&R and A&C committees of the JST. Conforming with the informal JST motto of “making safety cool”, the PR committee functions as a medium of communication to establish safety as a common topic of research conversation. In addition to maintaining an active social media presence on Twitter (@UMNJST), the PR committee has utilized a variety of innovative means to inculcate safety into researchers. In 2016, the PR committee started publishing “stall wall moments”, which are letter-sized safety posters installed in the restrooms of both departments. A repository of all publications from the PR committee can be easily accessed through the JST website. The PR committee has also installed large (3 feet × 2 feet) safety posters across building hallways, stairwells, and common areas describing general safety procedures such as hazard pictograms, glove choices, data management, and building emergency evacuation plans. The committee strives to promote colloquial safety-related readings to encourage daily communication to further strengthen the safety culture. Surveys have consistently shown that “stall wall moments” and posters are efficient means of communication which convey available safety resources and provide commentary on relevant safety incidents to the student body on a daily basis. The PR committee has allowed the JST to become the visible face of safety in the two departments making it easier for all researchers to approach safety, not with apprehension, but with an inherent curiosity to learn and implement self- and community-wide safety improvements
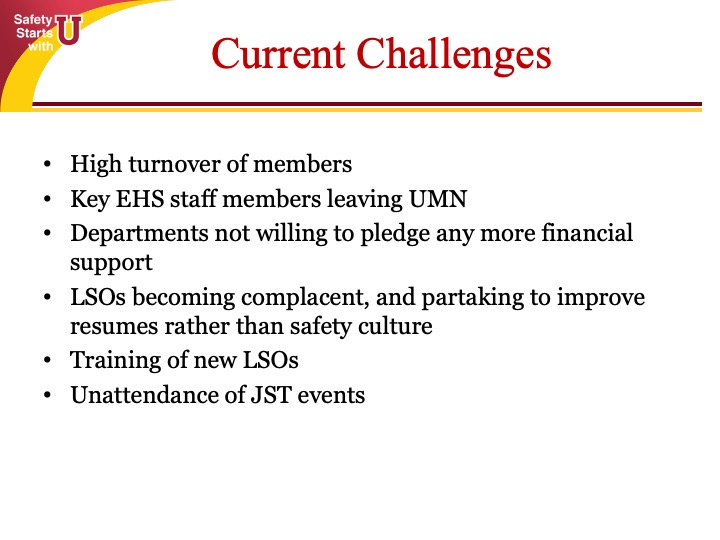
Promotion of the Safety Culture[bw][bx][by]: Academic safety is known to lag behind industrial expectations due to the lack of dedicated resources and enforcement as well as a deficiency of a strong safety culture. The JST periodically organizes industrial visits to the DOW campus in Midland, MI and the Valspar Corporation (now Sherwin-Williams) corporation in Minneapolis, MN. The visits bolster the attitudes of the visiting students about safety and provide them with opportunities to gain insights into developing new safety protocols at their home laboratory. Furthermore, this JST peer-to-peer model has inspired departments at other universities to set up analogous organizations to promote safety through a similar model.
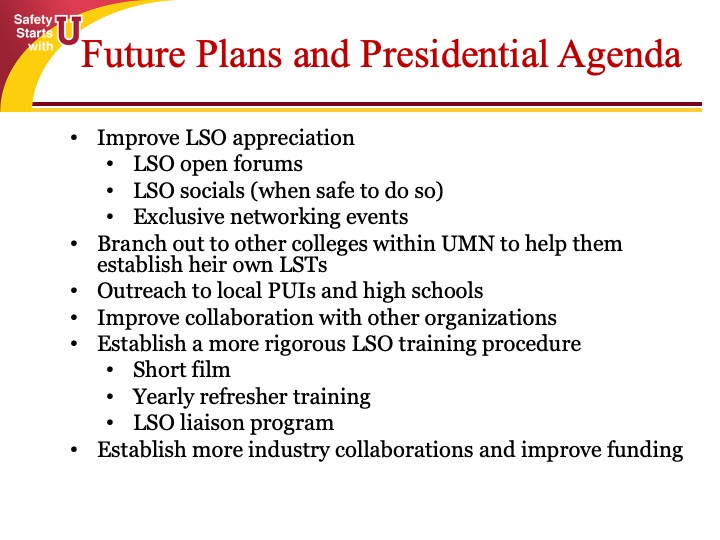
CONCLUSIONS AND OUTLOOK[bz][ca][cb][cc][cd][ce][cf][cg]
Although the JST is a well-established organization in 2020, several challenges inherent to academia remain unaddressed. The high turnover of laboratory members makes it difficult to perpetuate the safety culture and good safety practices. Enhancing participation from LSOs and non-LSOs in safety meetings also proves to be a difficult task. [ch][ci][cj][ck]The JST continuously works toward the development of innovative means to make “safety cool” and hence sustain the safety culture. The “inform and reform” model, i.e., the “Minnesota model” has been well supported by the feedback mechanisms to improve the information that is conveyed to researchers as well as ensure constant improvement in safety standards in the CEMS and CHEM departments. The feedback mechanism itself presents a new set of challenges including excess or lack of specificity of the questions[cl][cm][cn][co][cp][cq] and encouraging thoughtful feedback from researchers in addition to evaluation[cr]¨C96C¨C97C¨C98C¨C99C¨C100C¨C101C¨C102C of the JST activities provided solely based on a point scale¨C103C¨C104C.
[a]This work will hopefully be considered an added value to a person’s research education.
[b]I completely agree!
[c]Agreed!
And again this is another area where I feel that funding mechanism influences the degree of latitude afforded to graduate students in relation to their time allocation. Ones being supported off the research grant are often given less leniency for time spent not solely in pursuit of the grant deliverables.
[d]Agreed. Where you put the money is what gets the attention. Either (a) grant funders need to make safety education part of the grant or (b) the uni admin needs to step up and fund these efforts as part of functioning in the uni.
[e]Absolutely. The fact that we can allocate stipends for volunteers signals to everyone that this taken seriously and being supported by the higher ups
[f]Did anyone feel these concerns were legitimate? i.e. did someone has evidence that time was actually taken from research? Or was this just a general statement?
[g]Safety should be part of the research work. Tilak
[h]@jessica.a.martin@uconn.edu. While I wasn’t there at the time, I know of professors who in recent times have been worried about their students participating in student organizations in general. I think this worry comes up when students are involved in one of the JST committee’s rather than when serving as LSOs
[i]Jen Heemstra makes the point that the faculty member’s commitment should be to the student’s professional development, not the amount of lab time the students put in. JST committee work is an important professional asset when it teaches administrative skills (leadership, budgeting, communication)
[j]I know of advisors who don’t support their students taking up leadership positions outside of the lab. I am not surprised some of the faculty members started complaining about the time their students spend out of the lab.
[k]Agree with Monica. This varies quite widely. In terms of Ralph’s comment, it does come back to questions around the purpose of the institution: As a PI, are you primarily there to deliver students or primarily there to deliver data?
[l]I think many would default to the later response, as it influences future funding.
[m]I think that is the sad reality. Grad school on paper is about getting a degree and growing as an individual, but not every PI sees it that way
[n]I think it depends on how broadly you are considering the picture. This is constantly talked about in organizational literature. If you focus on product, you will make money in the short-term. If you focus on supporting your employees, you will typically make more money in the long-term. Better environment = more productivity if you are looking at the long game.
[o]The ACS did a study in 2014 of graduate education that is very interesting to read in light of this issue. The study was led by corporate science leaders and voted strongly for broader education rather than data-oriented training
[p]That is really interesting Ralph. Do you have a link to that study?
[q]What is the value of these stipends? For example, do the members do the JST activities INSTEAD OF teaching? Or are they additional supplements to standard funding mechanisms?
[r]Also, is there a means of judging whether or not paid JST members have “earned their pay” so to speak?
[s]The stipends are $200 per semester, so they do not replace teaching. The committee chair keeps track of attendance to committee meetings, of which there are usually five each semester. The member loses $40 for every meeting missed
[t]Are these solely researchers, or have there been other univ admin staff joining too?
[u]They have been solely researchers. We have tried to ensure that we stay student led so far. We do have a DEHS personal and department staff who support us, but at the end of the day the team is researcher led
[v]We have found that participation of and leadership from more permanent staff is quite useful.
[w]While it is important to have more permanent members stay up-to-date and interested in the LSTs, the thing that sets the LSTs apart from other types of committees is that it is graduate student and postdoc led. This has been incredibly important in order to encourage honest conversation and evaluation from those on the frontline in these labs.
[x]I agree with Anthony in that I’ve found substantial value in engagement and involvement with more permanent staff.
I’m not recommending a change in structure from a leadership and organizational perspective. But I do feel that having engagement and participation from career staff is value-added and can serve in areas of continuity and knowledge transfer.
[y]Our old DEHS staff representative was very essential to our success as well, and we felt a big hit when she left the university. Having that reperseenitve be present at our meetings and advocate for us was extremely helpful. The most important distinction is that they serve in a supportive role, but the organization as a whole is still researcher led
[z]Who does this representative tend to be? A scientist? Administrative staff person?
[aa]It is a DEHS administrative stuff. They usually have some background in science however
[ab]Additionally, do you have any sense what is “in it” for the company to be this involved? I have found that we struggle to get much traction in building relationships with local companies – beyond giving us tours of the facility (which is usually thought of as a recruitment opportunity to them so is typically run through HR).
[ac]I think it is more or less PR for them too. They employ a lot of grad students, so it does help them to have their future employees trained in proper safety practices
[ad]I suppose it may depend on how heavily they anticipate recruiting for 1 particular program at 1 particular school…?
[ae]Yeah they are very involved in the two department where we operate. They have recruitment events and even collaborations with some of our faculty
[af]At Cornell, I was able to arrange a safety-oriented tour of Corning labs for chem engineering students. They were disappointed that they didn’t get to hear about cutting edge research (aka trade secrets) as well as working expectations…
[ag]Well – if they thought they were going to hear trade secrets, they may need a bit more education on how companies run :). I have been on tours in which they were essentially led by HR & we didn’t get to see anything cool which were terrible. I have been on other tours that have involved researchers and we got to actually go around the facility and discuss details of the work. If our questions go to something proprietary, they would say essentially, “can’t answer that – but here’s what I can say.” Those were extremely valuable tours in terms of thinking about how companies operate and what possibilities existed for career options for researchers.
[ah]I have found that it takes an entirely different vocabulary to say what you are interested in doing in academia versus what you are interested in doing in industry.
[ai]Yes, the grad students were disappointed that they were being educated about safety vocabulary rather than technical fields where their strengths already were. With this in mind, I could have done a better job in setting expectations for the visit.
[aj]The unhappy response was “well, I missed a day in the lab for this”
[ak]I have found that our lab tours attract far more international students than domestic students. Everyone has expressed appreciation for the tours and the ability to connect – I definitely do realize that the students are going on the tours to make connections in companies (not for the love of learning about safety), however, I also think it is good that the two (safety + employability) are being shown together and necessarily connected to each other.
[al]We usually organize tours to Sherwin Williams that along the same lines. It about highlighting the safety practices there and also a recruitment event for the the company. We have gotten mixed responses are well in the past
[am]Employability = meeting industrial level expectation = part of a person’s research education?
[an]I think in an ideal world it would be, but safely safety adherence gets often overlooked in academic settings
[ao]There are also quite a few PIs who do not think of it as their job to prepare their students for work in industry.
[ap]There are quite a few PIs who wouldn’t know what industry needs. My master’s adviser went on sabbatical year to an industrial position and came back 6 months early because he and the corporate world didn’t get along
[aq]Do we even have a “definable” idea of what industry is looking for? Safety is too broad for those academics who have never worked in industry.
[ar]While I think that it is a good idea to get a feel for the “definables”, I also think a lot of the problem is actually centered around the basics: wear your freakin’ PPE; don’t do stuff in the lab without telling other people what you will be doing.
[as]Yeah I think the main thing that we got from DOW and Sherwin Williams was to have researchers go with a safety oriented mindset, and being willing to adhere to safe practices outlined by the companies. That is why the core of what we advocate is the safety culture above everything else
[at]Personally, it was weird for me to go from undergrad where you are constantly watched to grad where you are NEVER watched. The companies I have worked with, there was an expectation that people were going to be around sort of keeping an eye on you, but it was also your job to be an adult and communicate with others. Personally, I found this REALLY GREAT because I learned so much more from the people around me.
[au]This seems like a very doable, yearly investment. Any idea on ROI?
[av]Are there any critical “donations” of space, resources, etc?
[aw]I am assuming that this amount does not include the stipends. 🙂
[ax]What do you mean with ROI? In terms of space, we have not needed any dedicated space so far. Any supplies that we have needed to keep we have kept in a box that one of the committee members keeps in one of their offices.
[ay]Yes that is correct Jessica
[az]ROI = return on investment
[ba]I would imagine that all of the press and attention UMN gets for this work is likely the ROI to be expected – and all of this attention resulting from a few thousand dollars is likely viewed as remarkably good ROI.
[bb]I agree with Jessica. I think the department is very happy with the exposure that we get and uses us a recruitment device. I also think the simple fact that people generally feel safer in their lab spaces is well worth it
[bc]Are these costs solely operational/administrative, and not reflective of any other incentive expenditures (e.g. monetary awards)?
[bd]The costs are split between posters, awards, and food. There is a figure in the paper that breaks these down in more detail
[be]Is space limited? If not, is there interest for participation from other departments/organized research units?
[bf]The space is not at all limited. We have currently started a new committee dedicated to outreach, and we plan to start inviting students from local PUIs
[bg]Excellent, I hope that others find value and choose to participate.
[bh]I hope so as well!
[bi]It would be interesting to see the list of topics covered where student interest was the greatest. Also, are these meetings mandatory or optional for students in these departments?
[bj]We do send out surveys after these events to gauge interest, but we do not get a lot of response. These events are mandatory for LSOs, but open to all researchers
[bk]While I know it doesn’t “feel” like data gathering, I have found it far more useful to have our JST members (and EHS staff) floating around during events eavesdropping on conversations and explicitly asking for people’s feedback rather than handing out surveys. Not only do we get more response, the responses are actually much more useful and informative – especially when I engage people who have been “voluntold” to be there but are clearly not enjoying it. You gotta be ready for the real criticism with that approach though :).
[bl]Yeah I try to do this during our events where we have group discussions. I participate as a researcher and not as the president of the JST, and I think that helps me gauge people’s attitudes a little bit. This was easier when everything was in person though
[bm]Is this lab spaces or lab groups? (i.e. my 1 lab group has 3 separate lab spaces that are all situated next to one another – the 3 spaces are inspected separately by EHS).
[bn]We do it by groups. The idea is that each group gets a review of how safe they are that they can discuss together afterwards
[bo]Is there is any checklist for the walkthrough, how do you gauge the safety improvements
[bp]Yes. We have a sample sheet in the SI. It is constantly being revised and each category has a detailed rubric. The A&C committee also analyze the results each year and reports that information to the heads of the two departments
[bq]Have these results been used to identify department-wide pain points or issues that are more appropriately addressed on a department level or university level – rather than just individual lab issues?
[br]We have identified issues on the department level that we have addressed or are currently addressing. One big issue in the past was cluttered which we did an event targeting in the past and did a good job of minimizing. We have also had issues come up with electronics and old waste, and so we have brought up those issues in our events. We are currently working on creating hazard specific walkthrough rubrics
[bs]This is an excellent program!
[bt]Thank you!
[bu]It is really good to see that this produced an effective feedback loop.
[bv]Yes we are very lucky in that we have a lot of support from the departments, and that they are willing to listen to the issues that we bring up and try to address them
[bw]Have there been or are there plans to expand to other departments?
[bx]We are currently working in talks with the college of pharmacy to try to implement a safety team there. There are the closes to us in terms of research, but they have their own set of challenges such as being spread out all over campus
[by]This is an interesting example, in that pharmacy’s have product safety certification requirements as well as lab safety concerns. This might provide another angle to foster in that department
[bz]The ultimate purpose of a JST is to inculcate safety into the students as they progress in their careers. With about 8-9 years history in this project, is there any follow-up of graduates who are now a few years into their post-graduate career?
[ca]Great point!
[cb]I don’t know a lot of the original organizers, but I do know of a few. One of the DEHS positions have been field with a previous member of the JST, and there is actually another DEHS position that I know a graduating member of the JST is seeking. I also know that several members ended up in different industries where they continue to advocate for safety in their new roles. Good point though, I will try to reach out to some of the past members though and compile a list of stories
[cc]This is a really good idea. While it is neat to see some of these folks become safety professionals, I think it would be really important to see some of them go into more traditional roles but have their JST experience influence how they act in that role.
[cd]Are the opportunities associated with JST involvement discussed with potential students? Or when recruiting new faculty?
[ce]I hope, and the reason I strongly support JSTs, that the next generation of PIs and lead scientists include safety in their science view. Measuring that will have a strong indication of the success of the JST endeavor.
[cf]@Ralp Stuart, One of our biggest recruitment tactics is to say that involvement in the JST looks great on a resume and allows you to network with safety professionals.
[cg]@Neal I completely agree. We have gotten to the point where the JST is embedded into the fabric of the two departments and taken for granted. Our biggest measure of success has been the surveys that we send out, and how people feel about the safety conditions of their work environments
[ch]What kinds of things have you tried?
[ci]More interactive activities such as safety demos was a big hit. We have also tried to do hazard specific panels as well as invite outside speakers. According to our rules we are supposed to penalize LSOs who do not attend, but we have not implemented that because we didn’t want to add another source of stress to our LSOs during a pandemic
[cj]I would think it wouldn’t make sense to have penalties for non-attendance – goes against the spirit of the whole thing! I recall Texas A&M’s team used “Safety Moments” to start meetings that were focused on a particular technique or piece of equipment – for example, they started with glovebox safety. After kicking off with the Safety Moment, they would open it up for everyone to share questions, ways they had dealt with different challenges, etc. I really liked this idea because it was more specific for people who had those particular challenges so I would think they would get more from it as opposed to always focusing on the safety stuff that all of us share.
[ck]That’s an interesting idea. We try to start our events with safety moments, and all of our departmental seminars also begin with safety moments, but we do not open the floor for discussion afterwards. In the past we have had specific topic events such as Schlenk lines, glove boxes, vacuum pumps, etc, and those we do get good attendance for
[cl]This is a core skill for professionals in general and safety professionals in particular to develop. It is not easy and is done by trial and error. So it is good to hear that this is being experienced at the grad student level
[cm]Yes we are constantly improving our skill level. The big issue is that a lot of the lessons that we learn get lost due to the high turnover rate that we hava
[cn]There are commercial half day and full professional development courses around these issues available that can be useful in the early stages of ones career. Perhaps the departments could support scholarships to them.
[co]That would be an awesome way to bolster the “value” of high participation in the JST as well.
[cp]That is a good idea. I think the department is not willing to pay any extra money right now due to budget cuts and COVID, but potentially when the pandemic is over we could pursue that route
[cq]There is also the possibility of seeking out what is already happening and then inviting/incentivizing your LSO folks to go. So many of the issues that come up for JSTs have to do with communication, handling difficult conversations, managing up, etc – and I certainly know there are other departments at UConn who do a much better job of creating these events than my department does. The events are typically open to all departments – although I have been at PLENTY of these types of events/trainings in which I am the sole Chem person (even though we are one of the largest departments on campus) and sometimes even the sole STEM person. If my Chair actually valued this type of training, even light encouragement from him could increase those numbers.
[cr]How did the recent incident impact the JST? Was there a sense of failure?
[cs]Which one are you referring to?
[ct]dec 4 2020 chemistry explosion?
[cu]Yeah there was definitely a sense of failure as a result of that incident. One the biggest one was that it took a lot of time for anyone to communicate what happened with us, and so it was months after before we could say something to the LSOs about it, which angered a lot of people
[cv]What was the cause of this incident, can you briefly explain
[cw]The fact that this delay in communication angered a lot of people is in itself progress! Stuff happens in our department all the time that doesn’t get discussed or shared in an official capacity – and no one is angry about it because it is just so normalized for us to not be in that conversation.
[cx]The researcher ran a Fischer esterification with two new substrates on a 35g scale. They felt safe because they had runt he reaction with different substrates on a similar scale in the past. The reaction involved adding propargyl alcohol to a sulfuric acid mixture and heating to 70C. after 30 minutes the reaction detonated. The researcher did not have a lab coat on and had several cuts and burns. Luckily there were other group members there who helped the researcher use the safety shower and then seek emergency help
[cy]I agree Jessica. It definitely is a step in the right direction. There is still room for improvement though!
[cz]Have you made any efforts to encourage feedback by a mechanism other than surveys?
[da]We have recently started doing a semesterly LSO forum. This in an event where all LSOs are invited to come together and share any issues that they are encountering