Presented by Sarah Zinn, University of Chicago
02/17 Table Read for The Art & State of Safety Journal Club excerpts from “Lessons Learned from the Creation and Development of a Researcher-Led Safety Organization at The University of Chicago”
The full paper can be found at: https://pubs.acs.org/doi/10.1021/acs.chas.9b00012
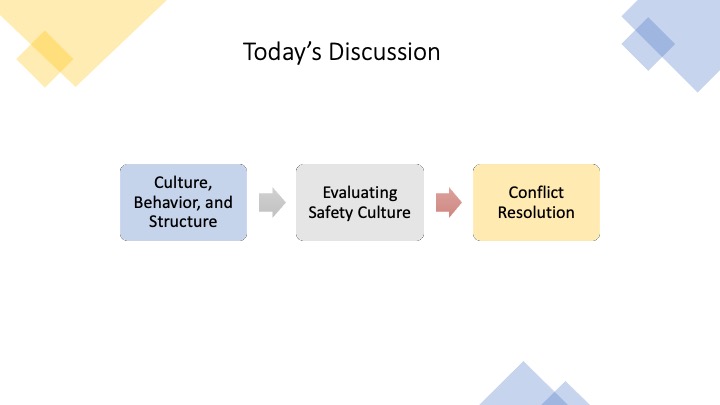
INTRODUCTION
“Safety standards and practices within academia have fallen well below those of their industrial and governmental counterparts due[a][b][c][d], in large part, to a relative absence[e][f] of the financial and public pressures that become driving forces within government and industry.[g][h][i][j] However, it has been shown that a strong safety-centric culture has a significant statistical correlation with a low occurrence of high-risk behaviors, low accident rates, high productivity, low absenteeism, and long-term institutional success. Considering these correlations and the numerous devastating accidents within academia, vigorous discussions about how to build and maintain academic safety cultures have been spreading across the United States. Numerous connections between strong, coherent, safety-minded leadership and the institution’s safety culture have been made, yet the unique and sometimes nebulous leadership structures within academia often complicate and fragment these efforts, leading to diffuse, sometimes conflicting, leadership[k][l] and, therefore, a primary emphasis on regulation compliance over collaborative, proactive engagement[m][n]. Thus, here we describe a case study of the implementation of a researcher-led safety team working to bridge the gap between safety administration, departmental administration, and researchers at The University of Chicago: The Joint Research Safety Initiative (JRSI).”
“Often, the ultimate goal of researcher-led safety teams is to strengthen the organization’s safety culture. While laudable, the realization of this goal is difficult both to achieve and to quantify since the underlying conditions are vague, intangible, and not necessarily consistent [o][p]with the observable artifacts. Thus, achieving this goal likely requires (1) many years, (2) significant personnel turnover, and (3) carefully planned methods of long-term measurement.”[q][r][s][t]
Working definition of safety culture
“The precise definition of an institution’s safety culture is ill-defined and varies greatly between fields. Herein, we will use Edgar Shein’s model of organizational culture[u][v], where we will use the term “safety culture” to refer to an organization’s shared beliefs, values, and attitudes regarding safety (underlying conditions) as well as the organization’s observable safety-related behaviors, policies, publicized values, and front-facing messages (artifacts)”
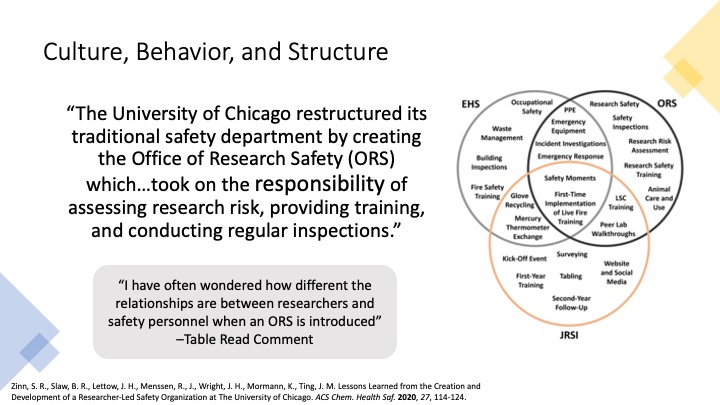
Conditions at The University of Chicago
“In order to understand the formation of our researcher-led team, it is first necessary to understand the context and history of safety administration at The University of Chicago. Prior to 2009, The University of Chicago’s safety administration consisted of the traditional Environmental Health and Safety (EH&S) department which was broadly responsible for the health, safety, and environmental compliance of the educational and research community at The University of Chicago. However, in 2009, Malcom Casadaban, a University of Chicago Associate Professor, died after being exposed to Yersinia pestis and contracting the plague; a mere two years later, a university researcher was hospitalized for surgery and antibiotic treatment after being exposed to Bacillus cereus.[w][x][y][z][aa] It was in response to these startling exposures that The University of Chicago restructured its traditional safety department by creating the Office of Research Safety (ORS) which reported directly to the Vice President of Research and National Laboratories and took on the responsibility of assessing research risk, providing training, and conducting regular inspections. This newly created ORS[ab][ac][ad][ae] took an active role in supporting researchers and sought to empower researchers in strengthening safety culture by implementing a variety of programs, including creating an online anonymous incident reporting tool and publishing a publicly available lessons learned repository.”
“In alignment with the key principles of safety teams discussed in the literature, the JRSI does not assume the enforcement roles or hazard training responsibilities that EH&S and ORS assume. Instead, we work to facilitate dialogues between the various administrative, student, and researcher groups within the PME and the Department of Chemistry[af][ag]. We work hand in hand with these various groups to make resources easier to access and to involve researchers more directly in conversations about safety.”
IMPLEMENTED PROGRAMS

Developing Organizational Structure
Initially, “a subset of attendees interested in the practical development of a safety team began meeting monthly with administrators from EH&S and ORS[ah][ai][aj]… During this time, the JRSI continued to operate under a mostly informal structure…”
“As we started implementing our programming and as our organization began seeing member turnover, we [started] providing a small quarterly supplemental stipend [ak][al][am][an][ao]for members of the JRSI…to ensure the JRSI’s continuation.”
“we began our first round of active recruitment by sending an application to apply for board membership via email; in this solicitation, we detailed the potential benefits of participating in our organization, including distinguishing one’s CV with professional service, obtaining low-stakes experience in a safety career path, working toward the development of one’s department, and the aforementioned supplemental stipend[ap][aq]. During this first application round, we received 14 applications—8 from the PME and 6 from the Department of Chemistry[ar][as]—with 50% of applicants being participants in our first Peer Lab Walkthrough event and 43% of applicants currently or previously serving as LSCs[at][au][av][aw][ax] (21% of applicants were both participants in the Peer Lab Walkthrough and LSCs). During this application cycle, we brought on 7 new members for a new total of 10 board members.”
“The organization’s main leadership comprised the 3…members…[on] an Executive Committee made of two Co-Presidents and a Treasurer. The members of this Executive Committee are responsible for the general functioning and organization of the JRSI and also serve as Committee Chairs for four key areas of the JRSI’s work: The Publicity Committee, The Survey Committee, The Education Committee, and The Finance Committee.[ay][az][ba]”[bb][bc]
Lessons Learned
- “Having upper administration buy-in was crucial to initiating dialogue with faculty, ORS,[bd][be] EH&S, and researchers, and as such it was a fundamental springboard for the development and successful implementation of nearly all of our programs.”
- “the early development and organization of a shared document repository proved to be essential for efficient operation…[and the] consider[ation of] how documents will be handled with future board turnover.”[bf][bg][bh][bi]
- “our new, more organized and departmentalized structure enables us to pursue a much broader set of initiatives; however, if the realization of a formalized structure is not yet feasible in the initial process of setting up a safety team, we recommend at least formalizing executive positions as a method by which to keep the team organized and driven.”
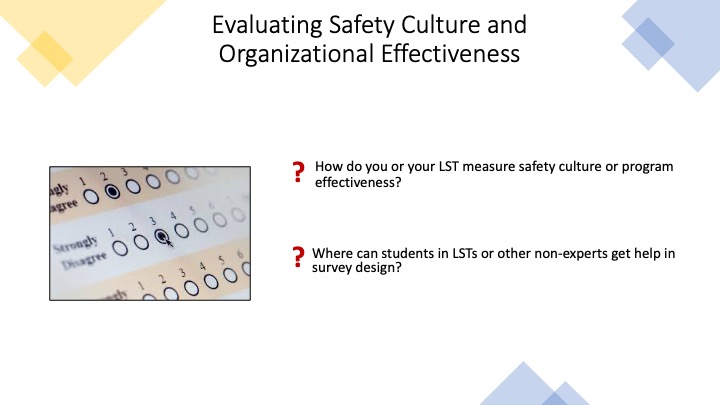
Evaluating Safety Culture
“The major and subsisting effects of our implemented programs will likely not be seen during the tenure of the original JRSI team.”
“in order to appropriately gauge the effectiveness of our Initiative and our programs on positively impacting the culture, it is imperative to utilize appropriate and robust methods to probe not only the artifacts of a university’s safety culture but the underlying conditions as well.”
“to make conclusions on the state of The University of Chicago’s safety culture and to identify specific areas that could be targeted for improvement…we developed a short initial survey…for which we offered no incentive to respond. Though we were able to glean a fair bit of information from this initial survey and were able to use it to internally motivate programming…our failure to obtain formal Institutional Review Board (IRB) exemption or approval prior to surveying precludes us from sharing the survey results with external communities.”
Lessons Learned
- “One of the most surprising and important takeaways from the implementation of the JRSI was the lessons learned on the appropriate way to [bj][bk][bl][bm]conduct this type of surveying. Since it is likely that most members in a researcher-led safety team will be students without a background in designing and administering surveys[bn][bo][bp][bq][br][bs] to human subjects, we believe that a discussion on survey design and implementation is neither trivial nor unimportant.”
- “having some initial surveying information permits the safety team to communicate with internal safety administration,[bt] departmental heads, and faculty about their institution’s specific needs and the ways in which a researcher-led safety team might benefit everyone, which may help to motivate both administrative and financial internal support.”
- “it may not be necessary to obtain IRB approval for surveying, as long as no personally identifying or sensitive information is gathered, and the results from the survey are only used for internal program-improvement purposes[bu]. However, any safety team wishing to share survey results with external communities at any point in time, like at future conferences or in peer-reviewed papers, should obtain formal IRB exemption or approval before beginning the surveying process and should keep in mind the mitigation of potential risks to participants and potential vulnerabilities of the target population”
- “while surveying LSCs resulted in valuable information, the biased sample only provided one limited vantage point of the greater safety culture…we highly recommend designing surveys that can be distributed to all members of the departmen[bv][bw]t, including graduate students, postdocs, undergraduates, and even faculty if possible.”
- “while in reality most surveys implemented by safety teams will likely experience multiple iterations, we highly recommend that the survey is as complete as possible as soon as possible so that annual resurveying efforts can be comparable; even seemingly small changes can create a different surveying experience which can significantly impact respondents’ answers”
- “We highly recommend consulting the literature on effective survey design before implementing large-scale surveys.”[bx][by][bz]
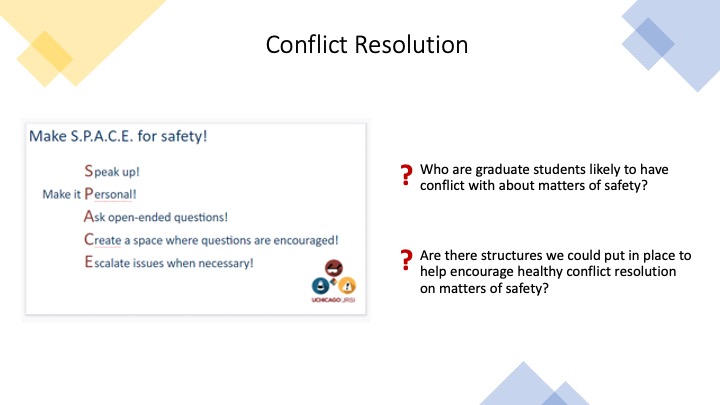
Facilitating Communication
“It is largely recognized that collaborative, inclusive interactions increase active participation and involvement within an organization. Furthermore, it has been concluded that insufficient collaboration, specifically between researchers and internal safety administration in academia, cultivates an overly top-down, largely compliance-based approach[ca][cb][cc][cd][ce][cf][cg] to safety.”[ch][ci]
“With the JRSI in its infancy, we hosted a 2 day kickoff symposium and vendor fair[cj][ck][cl][cm][cn] to officially unveil our organization, to reach a broad base of the community, and to begin forging interpersonal connections between researchers, safety administration, and departmental administration…Two days after the invited speaker symposium, we organized a safety-centric vendor fair. In addition to their normal marketing, these vendors performed safety demonstrations and distributed safety-related promotional items such as glove samples and informational posters.”[co][cp][cq]
“One creative and potentially high-impact approach to fostering positive safety culture that we have seen implemented by other safety teams is to host a lab walkthrough event[cr]. Inspired by the UMN JST, the JRSI introduced a pilot Peer Lab Walkthrough [cs]in early 2019. This event was a friendly competition in the Department of Chemistry and the PME which was intended to promote safety innovation, to elicit camaraderie, and to encourage open discussions about best practices. The competition was a collaborative educational opportunity for research groups to share safety knowledge, creative solutions, and lessons learned without regulatory authority or the threat of punitive action[ct][cu][cv]… LSCs and graduate student researchers from both departments volunteered as judges (Figure 5A) to assess a dozen voluntarily participating laboratories (6 laboratories or 26% of active laboratories from the Department of Chemistry and 6 laboratories or 28% of active laboratories[cw][cx] from the PME at the time of the walkthrough, correcting for joint appointments). The JRSI, in partnership with ORS, established a detailed scoring rubric[cy][cz][da] adapted from the one used by the UMN JST… After all laboratories were assessed and scores were tallied, the JRSI hosted an awards ceremony[db][dc], newly developed by the JRSI, and gave prizes to the highest-scoring laboratories[dd][de]”
Lessons Learned
- “We found the kickoff symposium and vendor fair to be a highly effective means by which to formally and impactfully introduce a new safety team to both internal and external communities. By organizing this larger-scale event which explicitly highlighted safety communication, we were able to generate a concentrated amount of interest and word of mouth, thereby solidifying a concrete starting point for our safety team”
- “While soliciting volunteers for the Peer Lab Walkthrough was essential to the program’s mission of facilitating communication and idea-sharing, their training was not trivial; though all of our judges expressed comfort in using our scoring rubric [df][dg][dh]after the in-person volunteer training, many questions arose during the walkthrough regarding how specific situations should be assessed, and some volunteers found the process of initiating the walkthrough awkward.”[di][dj][dk]
- “This can be done by using hands-on training, like through the use of a model laboratory rather than relying solely on electronic presentations,[dl][dm][dn] and by running through a full example of what to expect in a real walkthrough. With a sufficient number of volunteers, we also recommend having multiple volunteers walk through the same lab to help alleviate scoring inconsistency.[do][dp]”
Defragmenting Safety Resources
“A 2012 report by the Safety Culture Task Force of the ACS Committee on Chemical Safety identified several key barriers to achieving a strong safety culture, many of which involved fragmented infrastructure,[dq][dr][ds] support, resources, and educational materials.[dt][du][dv]”
“In the development of our website, we worked with safety administration to identify and clarify the disparate but related safety resources, both internal and external to our university, and coalesced them into a single accessible portal where all members of our constituency—researchers, undergraduates, teaching assistants, faculty, safety administrators, staff, and visitors—can navigate our broader, more complex infrastructure with ease.”[dw]
“From our initial LSC surveying, we came to realize that there were no formal guidelines provided to LSCs that detailed their responsibilities; since it is extremely difficult to perform the job well without a clear understanding of what exactly the job entails, the JRSI worked closely with ORS and EH&S to standardize the minimum required responsibilities of an LSC.”[dx][dy][dz]
“Defragmenting safety efforts and resources is a time-consuming task, but one which can offer clarity in how to best impact the university safety culture by forcing[ea][eb][ec][ed] involved parties to comb through the institution’s available resources and to interface broadly with the institution’s artifacts.”
Educating Researchers, Teachers, and Safety Contacts
“In an effort to make the most efficient impact on our University’s safety culture, we identified and targeted two key demographics—LSCs and first-year graduate students—and developed interpersonal training programs and support systems for them.”
“…we created an original program to develop safety-minded interpersonal training for these targeted key demographics. We strategized that incoming students can be strong drivers of cultural change in that they have not yet been exposed to the existing institutional safety culture; this, in combination with the fact that they still have many years of research ahead of them, may make matriculating graduate students an impactful demographic for working on long-term cultural change.“
“…we developed a training[ee][ef][eg][eh][ei][ej] [ek][el][em]for first-year students aimed at developing the soft skills required [en][eo][ep][eq]to communicate effectively and to contribute to a positive and supportive atmosphere around safety.”
Table Read Comments
[b]Whether they should or should not be relevant pressures is a separate question entirely. You can find information about this in the Safety Culture Taskforce 2012 report.
[c]I can look this up later (sorry if I’m just un-informed here) but do you know off hand if this is a re-occurring report and if it is how often it occurs?
[a]Were they ever at the level of industrial and governmental counterparts? How is this level measured? Is there data for this? Should financial and public pressures be the relevant driving forces for the academy?
[d]Melissa, to my understanding there has not been another report since 2012.
Dominick, it is also worth noting that much of the communications about safety culture improvement and safety administration improvement in academic settings across the country occurred as a response to massive fines and felony charges at UCLA after Sheri Sangji’s death. These financial and social/legal pressures have absolutely been a driving force in academia, and so has the absence of them.
[e]There are many financial and public pressures in academia, but they are different driving fources from government’s and industry’s
[f]Agreed.
[g]Are there any citations or references for this claim by the JRSI? Do we know that it is due “in large part” to lack of financial and public pressure? And that those are indeed driving forces in gov’t and industry? And that it isn’t other large factors at play? I’m skeptical of this broad claim.
[h]I’m struggling to understand the use of quotes on each paragraph. Is that on purpose? Or an artifact of it being a Google doc? Who is quoting whom here please?
[i]You can find information about this in the 2012 ACS Safety Culture Taskforce report. All quotes here are directly from the paper cited at the top. There are no direct quotes from any other source. The information in this paper was synthesized from various different sources, which are indicated by in-text citations in the paper cited at the top.
[j]See my comment to Dominick above for more:
“it is also worth noting that much of the communications about safety culture improvement and safety administration improvement in academic settings across the country occurred as a response to massive fines and felony charges at UCLA after Sheri Sangji’s death. These financial and social/legal pressures have absolutely been a driving force in academia, and so has the absence of them.”
Industry hasn’t always had incentive to drive safe practices, particularly in the early days of heavy expansion of chemical industry in the early 1900s (some corners of industry still don’t have substantial enough financial, social, and legal pressure to be interested in driving safe behaviors/environments—see meat packing plants, for instance). As some pressure was put on industry to do better to avoid worker comp suits, other legal fees, and fines, it became a bigger financial interest for these companies to proactively prevent accidents. The incentive structure is quite different in academia, and it wasn’t until fines and felony charges were seen by a major institution that academic institutions felt some substantial pressure to address these problems.
Of course there are many other very important and significant factors at play (indeed the entire point of this paper and of a safety team at UChicago is to address these other factors, which graduate students and post-docs may be able to manage some control over). The incentive structure of the institution to encourage and drive safety behavior (or not) is, however, a major influencer.
[k]Is this referring to conflict in EH&S uppers vs. PI or departmental staff/ faculty?
[l]Conflicting interests between different groups, like EH&S vs PI vs departmental staff, etc.
[m]Does anyone know if this emphasis on regulation compliance is or is not the primary driver for safety efforts at industrial or government research lab?
[n]It varies from place to place. Often in industry, there is also a strong emphasis on regulatory compliance as well. In industry, the literature shows that environments, where collaboration and worker-involvement are valued, have stronger safety culture and better outcomes.
[o]One of the goals should be professional development if we are going to be comparing our graduates to industry in order to make them industry ready. Since there are few accreditations given for graduate school degree, I am not certain of the best approach.
[p]Several of the ACS publications on Safety Culture have engaged chemists working in industry as content creators specifically because of the consistent complaint that PhD graduates aren’t “safety ready.” That being said, it seems to be a struggle to get really concrete information out of them by what is meant by “not safety ready.”
[q]One of the advantages of faculty researcher-led teams is continuity. This can certainly be built in to the JSTs, but there must also be institutional memory, and that is one thing that faculty can provide, maybe in the context of a champion?
[r]Where are the quotes coming from? The actual paper?
[s]Again, yes, all of the quotes are directly from the paper. There are no direct quotes from an uncited source.
[t]Yes, champions are important for a host of reasons, some of which are continuity and stability.
[u]Megan Gonzalez has in her dissertation tried to provide a definition of safety culture more targeted to academic laboratories.
[v]Yes, there are many different conceptualizations of safety culture
[w]Just wondering… it seems as though these accidents were in Biological labs. It is interesting that chemistry seems have taken the lead for JSTs rather than Biology, or is it a mix of disciplines?
[x]I’m also interested in this. Right now our Chemical Hygiene Committee isn’t very involved with our Biosafety Committee unless it directly involves chemicals.
[y]Great question! There is a lot of crossover between the work in biological departments and chemistry departments at The University of Chicago. The main reason that the chemistry department took the lead on the JRSI is simply because this is the group that was approached about attending the DOW Lab Safety Academy. We have had a lot of interest from Biophysics about getting involved in the team, even though they weren’t involved in the beginning.
[z]Is there any data on what percentage of active JST/LSTs are cross-departmental (overall nationally)?
[aa]I think this depends on how they are set up. A great question to explore!
[ab]The creation of the JRSI after the ORS would seem to imply that graduate students still felt as if there were needs not being addressed adequately.
[ac]I agree with this comment and wonder if it connects with the previous comment on the cited issues being biological lab heavy. Was there a disconnect between ORS focusing on particular hazards that left chemistry students feeling “left out” (for lack of better phrasing)?
[ad]I had this same thought but it would depend on how the group was started, if students wanted it because they weren’t feeling heard or if faculty wanted it to help empower students to develop a safety culture which is difficult by the ORS alone without student engagement.
[ae]There is quite a bit of time between the creation of ORS and the creation of JRSI. In practice, this means that all of the graduate students at UChicago have never known UChicago without ORS. ORS made improvements in the organizational structure, but by no means did it fill all holes.
As a side note, ORS covers all departments, not just chemistry or biology.
[af]once the JRSI was established, was an effort made to reach out to other departments?
[ag]Yes! Though to date, we haven’t yet expanded. Though there was initial interest from multiple departments, we didn’t have the bandwidth to incorporate other departments. However, now that our feet are more firmly planted, we’re thinking about how best to do this: incorporate them into one big team, or have a separate team in each department with good communication between them all? As of date, we have high interest from biophysics.
[ah]Was this a joint meeting or two separate meetings?
[ai]Does this mean that EHS did not have a member meeting with the JRSI regularly, other than these monthly meetings?
[aj]It was joint between the safety team, EHS, and ORS. At the time, we had only these monthly meetings with the greater ORS & EHS, but we always had a close point of contact with someone in ORS who functioned as a champion for us. She was in all of our email communications, all of our meetings, etc.
[ak]Who is funding this? And is this defined to equate to a certain number of hours per stipend period of labor dedicated to JRSI activities?
[al]I had same question and also wondered if money needed to fund activities is taken out of stipends or put to the side separately?
[am]Same question: where did the money come from? This would be a neat thing to ask for from VPR offices!
[an]Also interested in funding source.
[ao]The size of our board is capped at 10 members. Each member gets 500/quarter (including summer) contingent on active participation. Active participation is defined as attending 10/12 yearly hour-long meetings, joining at least one subcommittee and participating satisfactorily in that (as judged by the executive committee charing the subcommittee), and helping to plan the annual Peer Lab Walkthrough. We currently serve two departments—chemistry and molecular engineering. Half of everyone’s stipend comes from chemistry, half from molecular engineering. It is awarded by the deans, and does not come out of the JRSI’s pool of funding.
[ap]How was this funded?
[aq]The size of our board is capped at 10 members. Each member gets 500/quarter (including summer) contingent on active participation. Active participation is defined as attending 10/12 yearly hour-long meetings, joining at least one subcommittee and participating satisfactorily in that (as judged by the executive committee charing the subcommittee), and helping to plan the annual Peer Lab Walkthrough. We currently serve two departments—chemistry and molecular engineering. Half of everyone’s stipend comes from chemistry, half from molecular engineering. It is awarded by the deans, and does not come out of the JRSI’s pool of funding.
[ar]What was the demographic breakdown of time in program for these applicants? Was it primarily younger students or those beyond candidacy exams?
[as]I don’t have this information on me right now, but from memory it was a pretty health mix of all sorts of students. We had some pre-candidacy, some post-docs, and some mid-career. I think we received one close to graduation, but I am less sure about that one.
[at]I wonder why this is only 43%, I would expect that it would be higher because being involved in this program would help them fulfill their LSC duties. How many were previous LSCs?
[au]I’m not surprised it’s within this regime – I can imagine that the time commitment to serve as both an LSC and board member would be more substantial than some students would be willing to make.
[av]I’m not sure what @kalim863@gmail.com means here. At UConn, there is no set number of hours or duties to serve as an LSC (LSO) so whether or not an individual serves on the JST would have nothing to do with “fulfilling LSC duties.” It seems that it works the same way at Chicago?
[aw]43% really isn’t a bad number in student life and student activities circles…
[ax]UChicago functions similarly to UConn (as Jessica mentioned). There are no requirements for the number of hours spend as an LSC/LSO. Additionally, serving on the JRSI board does not impact one’s responsibilities as an LSC at UChicago.
[ay]Was there a reason that the committee chairs were not independent members?
[az]What is the plan for continuity and history?
[ba]@bader072@umn.edu can you clarify what you mean by “independent members”?
Dominick, we have a Google Team Drive that has an organized repository of all of our documents and our history and are working on securing another champion since our ORS representative passed away. In the meantime, there is a process of training to secure effective turnover.
[bb]Any long-term permanent members?
[bc]Yes, there are two members on the board (out of 10) who have been with the JRSI since the beginning. Both will be graduate soon, though.
We did have a member of ORS working very closely with us (functioned as a champion and a source of continuity), but unfortunately, she passed away a couple of months ago.
[bd]What is upper administration? To me this means the chancellor.
[be]deans and department chairs
[bf]Did you run into any issues with things getting lost after new leadership turnover or different documentation styles?
[bg]Because we still have 2 founding members on our board, we haven’t actually lost any documentation with leadership turnover. However, when the executive committee leadership transferred over to non-founding members, we definitely saw a lot of problems brewing with this (they could just ask the founding members, but eventually it will be lost information). Perhaps creating a sheet detailing all of the available information and documentation could help.
[bh]This is key to many volunteer groups and often not captured as an important piece.
[bi]upvote!
[bj]I have relearned this lesson the hard way several times. Sometimes the challenge is primarily language based – it is hard to get to the point of your question without slipping into jargon. However, there is also a need to understand what questions the surveyed population is ready to answer.
One way to figure this out is to use face to face focus groups to:
1) See how other people perceive the issue you are asking about
2) Understand what language they use to describe those issues
3) Figure out how to minimize the number of questions while getting the information you need.
This process pays dividends when the results of the survey come out.
[bk]I agree @Ralph. Qualitative methods such as 1:1 interviews and focus groups can provide depth and detail unavailable from surveys. All of these methods require a knowledge of effective design and evaluation techniques that many don’t realize is needed.
[bl]That is exactly the problem I have-who can we tap to help us with surveys and interviews other than doing our best based on the literature? There is no one on my campus.
[bm]@June Do you not have a Department of Psychology at your school? Or a School of Education? Or a Business School? These are common areas to find people who have survey expertise.
[bn]Would it be worth considering attempting to recruit someone from a different department who has experience with this to advise the team? If so, it may be worth what kind of incentive structure would make sense.
[bo]While we have a small number of people in the Department of Psychology at UConn who specialize in Industrial Psychology and some people at the Business School focused on the structure of organizations, I failed to find anyone who was willing/able to take the time to advise our team in this way – so it could be a tall order.
[bp]Before starting my PhD courses I opted to find a professional staff person well educated in survey design. She was quite happy to assist us and we found the process enlightening and the resulting survey much more useful and valid than our original draft (which we discarded). There are typically staff at uni’s who have this education and are able/willing to help.
[bq]It was nice that you found someone who could. My point is that I could NOT find someone who was willing to spend the time on it.
[br]We paid professional survey people housed on campus to help with this. The results were more statistically robust, but less educational than more informal approaches. Industrial Psychology people do tend to be quite busy with bigger money questions (e.g. maximizing workforce productivity).
[bs]We had someone in Industrial Psych who worked with a group of undergrads to examine Safety Culture within the kitchens on campus! That is why I thought he would be good to approach. He gave me a few useful things to look at & think about, but was unwilling to engage in a more productive way.
[bt]This is a very good point. My surveys have generally been cross-institutional, so there is a less well defined audience for the results
[bu]Always a good idea to have the blessing of the IRB. I know for the surveys that my students do, they always seek IRB approval, in case they want to publish the results. De-identifying is necessary, but a good IRB will provide examples of how to do it well, and will critique the techniques used.
[bv]These are likely to be separate surveys based on separate focus groups; don’t forgot to include support staff (administrative and technical) in this list. They often have the institutional memories that other portions of the community don’t.
[bw]Great points!
[bx]Very good point, and very true! This is especially true for surveys that might be pre-post or that want to be shown to be valid instruments. The methodology for making “valid” surveys is also in the literature.
[by]I agree wholeheartedly @dominick! Many surveys are poorly designed and constructed.
[bz]And when they are designed for statistical validity, they often stray from the content of interest. “Trending destroys fidelity”.
[ca]EHS can be in a tough spot with this. They are responsible for compliance and as such, it often needs to be where they focus – especially if they have limited resources.
[cb]It is mentioned earlier that a separate ORS was established. We don’t have an ORS at my school. I have often wondered how different the relationships are between researchers and safety personnel when an ORS is introduced.
[cc]ORS is only tangentially involved in EHS for many institutions. ORS might also bear responsibility for funding and grant opportunities and oversight. That tends to be a BIG deal and they just want EHS to “be sure we are in compliance” because “being out” can cause loss of funding.
[cd]I thought the Office of Research Safety was specifically designed to assist researchers in conducting their research safely – i.e. the stuff EHS often doesn’t have the time to do. Am I wrong in this? If not this, then what do they do?
[ce]ORS tend to arise when the administrative side (facilities or risk management) get frustrated with the academic side and vice versa. My experience is that the personalities involved are the primary driver of successful colloborations across this aisle
[cf]I agree with Ralph. ORS may also have oversight of hospital/patient research safety. Those tend to get more attention than engineering or chemical safety.
[cg]There’s a figure in the paper that explains how the responsibilities of EHS and ORS differ and overlap at UChicago
[ch]In most departments, there is also insufficient information about what each lab group is doing in terms of hazardous chemicals and operations, number of workers in the group and their statuses, the legacy and anticipated directions of their work
[ci]This is certainly true from my experience as well!
[cj]Vendors can be a valuable source of support for these efforts, particularly those with contracts with the institution who are interested in maintaining good relationships with the lab community.
[ck]We tried to do this at UConn, but our stockroom manager was really against it. She said that legally they couldn’t have relationships with vendors that were too close. I was baffled as I have ATTENDED vendor fairs at other institutions (even in Connecticut), but she was adamant about it so we did not pursue it at the time. Anyone ever heard of this?
[cl]I have not. Unless the state of CT is way off the beaten track in terms of vendor practices, this sounds like an individual concern. That’s the purpose of the state bidding process – to protect the vendors from “too close” relationships
[cm]We do vendor fairs usually once a semester (sometimes once a year), so I don’t understand this.
[cn]Yeah – I don’t think it is a state issue since one of the vendor fairs I attended was at the other university in CT (you know….Yale….).
[co]Was this provided for free to the University by the vendors?
[cp]Yes, it was. Indeed, we found out afterward that vendors will actually pay you to host a vendor fair. Whoops—missed opportunity for safety team funding ):
[cq]Whoa! That’s great to know! We’ve been trying to set one of these for our safety break event that we typically host in May.
[cr]These can be very engaging initiatives to facilitate safety culture efforts. It is nice to see it done and imitated by others. 🙂
[cs]This helps to address the problem mentioned above about collaboration and knowledge of other labs operations and concerns
[ct]This I believe is one of the effective ways of building a safety community within and between departments.
[cu]We’ve been doing peer walk throughs since 2012. I like the competition aspect. I’m guessing that it caused more groups to take this more seriously and look more deeply. What were the prizes? Again, who sponsored the prizes?
[cv]It very much did. Much of the department was abuzz after the winners were announced and the prizes were handed out. We had a $500 prize to the winning lab (across both departments), and a $250 prize to the top-scoring lab in the runner-up department and the second-scoring lab in the winning department. These awards were provided by the deans. We also gave out bonus awards for creative things we saw in the labs that weren’t acknowledged by our rubric (like a cool color-coded tape system to designate chemical-free and contaminated spaces). They weren’t monetary, just recognition. This year, the deans have doubled our available award money because of demonstrated success. People were also highly interested in the award ceremony, which we initially weren’t sure about! (:
[cw]Since the publication, have these walkthroughs been repeated and has % of labs participating changed?
[cx]Sort of! We started the second round of walkthroughs in winter 2020 and nearly doubled participation! Unfortunately, we had to cancel the event because of COVID, but we’re now working on revamping a virtual walkthrough and reaching out to the many labs and volunteers who signed up last year.
[cy]Is this rubric open/ accessible?
[cz]Yes! It is included in the supporting information (which is openly accessible) here: https://pubs.acs.org/doi/full/10.1021/acs.chas.9b00012
[da]Thank you so much! I had not yet looked at the supporting info 🙂
[db]Do you think having a more publicized way of acknowledging winners helped encourage future participation and heightened safety compliance? Did you see attendance at this ceremony restricted to the participating labs or more global participation?
[dc]I can’t speak to whether it heightened safety compliance on such short terms and without good measuring metrics, but it absolutely encouraged future participation and interest. Participation nearly doubled the next year, and people were chatting about the award ceremony for a while after. There was more global participation than I personally anticipated, but it was definitely mostly participating labs. We had deans and department chairs speak at the event, and had the department chairs boost our invitation email as well
[dd]What were the prizes? Was it a motivating factor?
[de]$500 / lab award for first place, $250 / lab for two runner-ups. The money was to be used for a lab event of their choosing. It seemed to be a major motivator, initially, though we were not able to survey. I can say that participation doubled the next year.
[df]A scoring rubric or some checklist is a good idea, as it doesn’t come across as capriciously walking through the lab looking for safety violations. Providing the rubric or checklist ahead of time also helps focus things like lab clean up.
[dg]lesson learned for me here. I did not take a rubric for my first set of lab walkthroughs. Checklists create a baseline.
[dh]We did indeed provide the rubric to the lab ahead of time!
[di]This is a major science education opportunity, so professional scientists often visit other people’s labs and need to be comfortable in asking questions to make the visit as productive as possible for both the hosts and the guests
[dj]I agree that this is a vital learning moment and should happen more often.
Has this been attempted again?
[dk]The Univ of New Hampshire EHS hires chem grad students to update chemistry dept chemical inventories in the summer and this is very popular with the students because they get to learn about the rest of the Chem Dept. they also avoid being stuck in one lab all day when they don’t have classes to get then out
[dl]Videos showing model situations could also be useful from the perspective of minimizing meetings (especially for members who have participated longer and feel more comfortable with the material and are less inclined to participate with a hands-on training).
[dm]I have seen a variety of videos about safety inspections with many different tones and attitudes. they are very hard to do.
[dn]I agree – I think having a video very specific to the safety rubric is most helpful versus more generalized videos about safety inspections in general.
[do]One strategy that we found to be very effective at UMN was to have the LSO event taking place before the walkthroughs be a training event for walkthroughs. It was also a place for people to voice concerns about the walkthroughs, which allowed the committee in charge of them to adjust accordingly
[dp]I like this incorporation!
[dq]Can someone elaborate on what is meant by fragmented infrastructure? That part is not clear to me.
[dr]The Chemical Safety Board described it with a Swiss Cheese model. Not everyone on the same page and holes in oversight, among other things.
[ds]That explanation helps. Thank you!
[dt]it seems like we have lots of educational materials, what is often lacking is those materials being presented in a way that impacts. A student led team might be able to present that information more effectively.
[du]Agreed. Our department’s approach to safety before was “here is a list of things you can read.” TBH, I never read a single one before I started working on these things because I had no direction in terms of what was actually useful for me to read.
[dv]Also agreed! However, there are also cases where resources are lacking. For instance, there were no resources (training, reference, or otherwise) for Lab Safety Contacts at our university.
[dw]I think this is such a good idea. Having all safety resources in one easily accessible place would really help to build general safety knowledge.
[dx]This is a problem that we are dealing with as well at UMN. We have an LSO guidebook that we are in the process of overhauling, and we also have an annual LSO training meeting, but many LSOs still feel lost early on. We are attempting to implement an LSO liaison program as well as a training video to overcome this probem
[dy]Communicating about safety in the lab is not easy for anyone and takes practice. Encouraging new people to get involved to learn about other people’s science while talking about safety is one way to help break the ice
[dz]We also implemented a soft-skills-training workshop with first-years to try and help them develop and practice effective ways to communicate about safety
[ea]forcing? Wouldn’t interest be a stronger driving force?
[eb]Yes, it seems like that would lead to resentment and people taking safety culture and the JRSI less seriously.
[ec]I think this quote has suffered by being out of place or bad phrasing? I think the idea is to “force” those who are providing the safety resources to present them in a more useful way for researchers to access….?
[ed]^Jessica’s got it.
[ee]Is this further explained in the paper? Interpersonal conflict seems to be a large reason for students not correcting their peer’s behaviors and I would love to learn more about how this training was conducted.
[ef]This is addressed in the supplementary information PDF pretty well
[eg]Thank you! I hadn’t looked at the SI yet so that’s very good to know.
[eh]Agreed. I also think a great deal of the tension between graduate students and their PIs (and how their PIs regard safety personnel) is a big part of what graduate students learn or don’t learn about research safety.
[ei]I agree to that tension point, Jessica. We’ve also had a lot of people report that they don’t verbally correct peers if they have in the past and haven’t seen changed behavior and that’s something we’re trying to figure out how to best address.
[ej]I introduced a competitive game into my lab when we had several undergrads during a summer to get people to wear their safety glasses. It was much more effective than me constantly saying “put on your safety glasses.” I can definitely understand the fatigue inherent in constant reminding. One of my fellow grad students used the gamification idea to get undergrads in a teaching lab to “bust” each other as well so it saved him having to do it all the time. I don’t really think the game could extend well to most safety practices though.
[ek]I like the peer aspect of this. We have a faculty-led course for first-year graduate students as well as EH&S face-to-face and electronic training, but I wonder if peer training sticks better, plus it allows students to ask more direct questions without feeling intimidated.
[el]We do peer training, grad to undergrads, during our lab audit teams. I think it works really well!
[em]I will be interested to see how the remote work covid requires inspires new training media. We are all going to be developing new communication skills (such as table reads)
[en]These are science skills as well as safety skills
[eo]I would push this to “these are great life skills to have”. knowing how to be supportive while recommending changes or improvements helps all over the place!
[ep]These are great life skills to have in general!
[eq]We need a course on effective communication and conflict resolution in safety!